BUILDING BASICS
BRICK & STONE
Abbot can provide solutions to correct concrete deterioration, brick and stone structural deficiencies such as misalignments, spalling, delamination, debonding, and building errors.
CONTACT US
ABOUT BRICK
BRICK DETERIORATION
Brick is a low-cost, fire resistant, and attractive building material that has long been in demand in commercial construction in the northeast.
However, brick is not fail-safe. Brick walls can fail due to freeze/thaw damage, florescence, corrosion of metal supports, or differential movement between the wall and its structural support.
Signs of brick deterioration include:
- Stains, cracks, or missing mortar
- Delaminated brick
- Efflorescence
- Broken or loose bricks
- Deterioration of metal supports
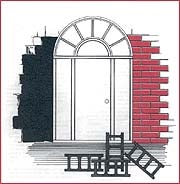

BRICK WALL TYPES
There are three basic categories of masonry brick walls: solid, cavity, and veneer.
Solid walls are two or more layers of brick held together with metal ties or header bricks laid perpendicular to the plane of the wall. Solid wall strength is a function of wall thickness, brick and mortar durability, and the strength of the mortar bond.
Cavity walls consist of an outer layer of brick attached to an inner support, and separated by an air space of two to four inches. The inner support may be another brick wall, a concrete block wall, or poured concrete. Cavity walls may be load bearing. The cavity wall is an ideal masonry system for preventing water penetration as the air space itself acts as a water barrier.
Veneer brick walls are typically a single layer of brick tied to steel or wood studs. The single layer wall has low insulation value. Insulation is attached to the studs and is not incorporated within the masonry.
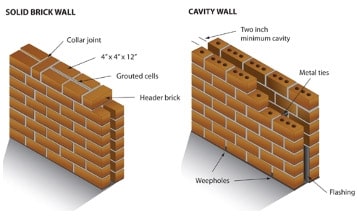
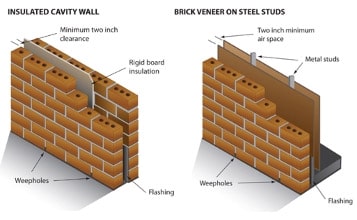
BUILDING WITH BRICK AND MORTAR
In building a brick wall, when mortar contacts brick, capillary action draws the dissolved (hydrated) lime and cement into the brick pores. As the mortar hardens, a fine web of mineral crystals bonds the brick to the mortar joint.
WATER PENETRATION: BRICK’S ARCHENEMY
The most common source of masonry brick failure is water penetration, especially in our colder northern climate.
When water freezes, it expands. If this expansion takes place in the pore spaces of a brick or between the brick and mortar, cracks are likely to form and propagate. With additional expansion cycles, the severity of the cracking may increase until the damage is repaired or the wall fails completely.
Water also carries salts into walls, either leached from cement in the mortar or percolated from the ground. As the water evaporates, salt crystals (florescence) form either on the surface of the brick (efflorescence) or within the pores of the brick (cryptoflorescence). Efflorescence is unsightly but does not usually damage brick by itself. Cryptoflorescence, however, can seal water into brick pores, causing expansion damage, or damage to the brick directly as the salt crystals expand.
THROUGH-WALL FLASHING: THE BEST DEFENSE AGAINST WATER PENETRATION
Brick walls that are designed to shed water are most desirable. However, through-wall flashing provides the best defense against water penetration. Through-wall flashing is an impermeable membrane placed in the wall that extends from the sheathing, across the air space, and all the way to the exterior of the brickwork. Properly installed flashing keeps water from penetrating through a wall face. Through-wall flashing at grade level prevents water from seeping into the upper section of a wall from the below-grade masonry.
Flashing should be placed at all points where the air space is closed off. Standard building codes require flashing at the foundation, above window and door heads, at window sills, and where the roof of a one-story wing meets a two-story brick veneer wall.
Flashing should extend from the outside face of the veneer, through the thickness of the brick, across the air space to the backing, and then up at least 8 inches. The flashing should either extend up behind the water-resistant barrier or be attached to its surface with a termination bar. Flashing held back from the outside of the brick veneer — even just 1/2 inch — may allow water to enter the wall.
Flashing that is punctured will not perform as intended and should be torn out and replaced. Where flashing under a brick course requires more than one piece, flashing pieces should be overlapped at least 6 inches and sealed with compatible mastic.
Because the expense and difficulty of replacing flashing is considerable, only the best materials should be used. Sheet metals, bituminous membranes, plastics, and combinations of such materials are suitable for flashing. Aluminum and building felt should not be used.
COMBINING BRICK AND STEEL
The combination of brick and steel can create considerable differential motion. Because the flexural strength of steel is greater than the tensile strength of brick, building sway will crack the brick if not kept within acceptable limits. This problem becomes acute when brick veneer is placed over steel studs. Further, because steel tends to deform somewhat under its own weight, while brick steadily expands, insufficient wall expansion joints can result in crushed brick.
REPOINTING
Loose brick and water leakage are signs that a mortar bond is failing and that repointing may be necessary. Removal of existing mortar is the most critical step in the repointing process.
Standard industry practice is to remove mortar by mechanically grinding the brick joints with special diamond blades sized to the width of the joint. The depth of the cutting should be a minimum of 3/4” deep. Then the brick and joint should be cleaned and dampened. Depending on the depth of the joint, new mortar should then be applied in layers to ensure that it bonds well with the existing mortar and brickwork.
PAVERS
Brick pavers are commonly used as an alternative to plain concrete or asphalt in a variety of exterior hardscaping applications, including walkways, patios and driveways. Available in a variety of shapes, brick pavers resist to fading from the sun and deterioration from long-term exposure to the elements and do not require a seal coat to prevent staining. Their closed pores create an almost non-permeable surface.
RECENT BLOG POSTS
Proudly Serving Greater Boston
& Eastern Massachusetts
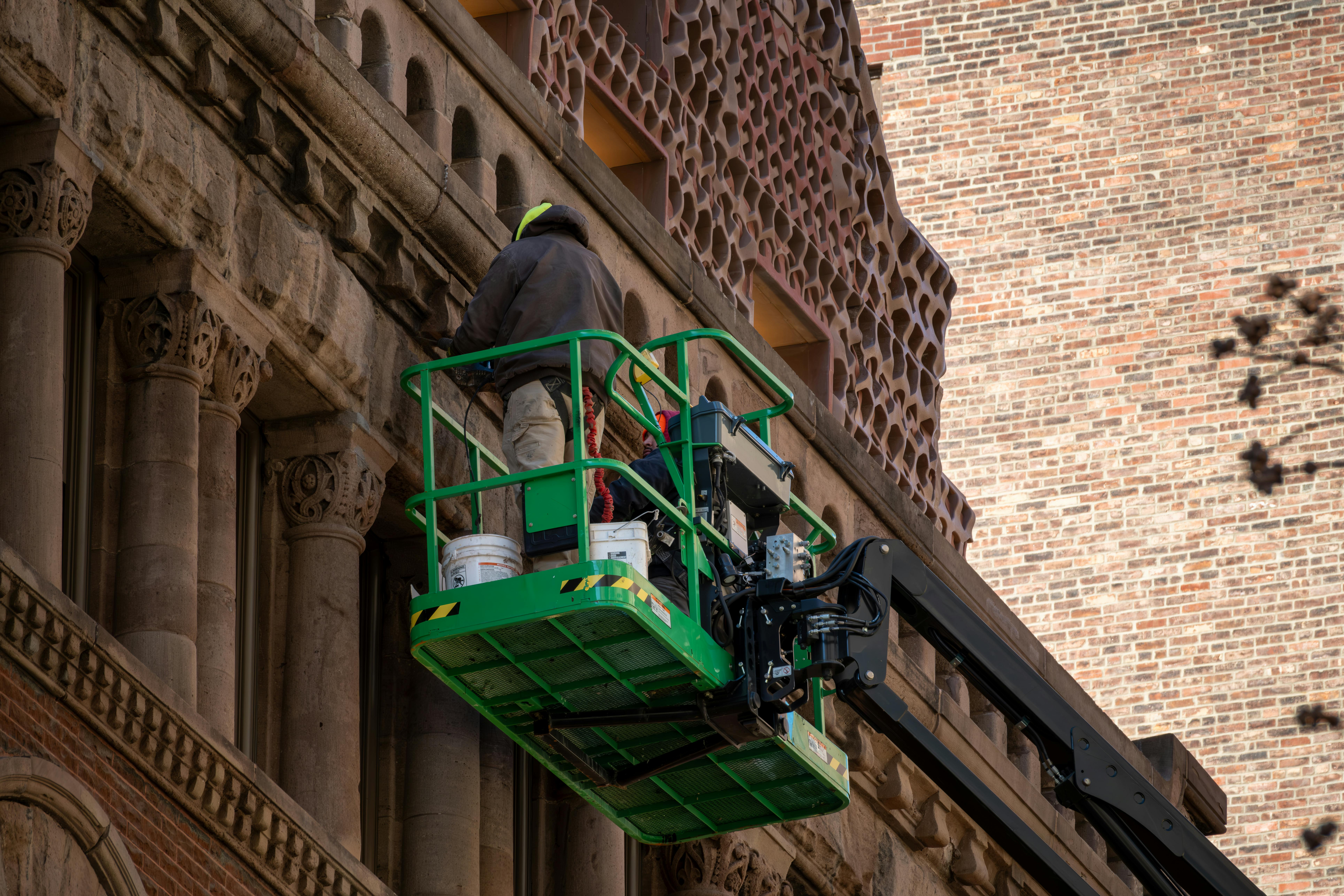
Three Unexpected Challenges of Masonry Restoration in MA
Beneath the surface, masonry restoration projects in MA frequently reveal unexpected challenges. These surprises can complicate timelines, increase costs, and require creative problem-solving.
Read More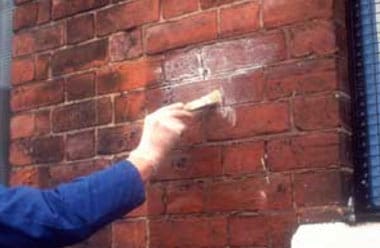
Protecting Commercial Concrete and Brick Repair with Weatherproofing
Weatherproofing is crucial to effective commercial concrete and brick masonry repair. Here’s how both surfaces benefit from this protective technique.
Read More